Converting plastic waste into fuel product introduction
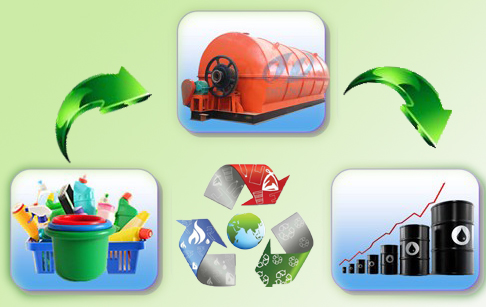
DoingGroup's plastic pyrolysis plant
Plastics play an important role in everyday life, as in some applications they are a conventional material with obvious advantages. Their light weight, durability, energy efficiency, plus faster productivity and more design flexibility allows for breakthroughs in different fields from unconventional energy, horticulture and irrigation, water purification systems and even space flight. Plastics are relatively cheap, and are easy to use and disposable culture. Plastic waste management has become a non-degradable property of a world problem because of them. Most landfills, assigned to plastic waste disposal, are approaching their full capabilities. Therefore, recycling is becoming more and more necessary. The DoingGroup's waste plastic pyrolysis plant is a device that converts waste plastic into fuel. It is a chemical process that breaks macromolecular plastics into smaller molecules of petroleum, natural gas and carbon black.
The main workflow of DoingGroup's pyrolysis plant for converting waste plastics into fuels:
Plastic pyrolysis plant working process
1. Collect a large amount of waste plastics for backup. This process can be contacted and cooperated with local waste recycling plants.
2. The waste plastic is fed into the reactor via an automatic pusher and the reactor is heated. The temperature rises to some extent and begins to crack heavy oil and gas.
3. Under the effect of high and low pressure in the equipment, heavy oil and gas enters the condensing system. After being cooled, it is liquefied into heavy oil and falls into the tank.
4. The deodorizing and deodorizing operation of the obtained heavy oil is the final fuel.
5. The carbon black produced during the combustion process will be automatically discharged outside the furnace through the underground sealed slag discharge channel, which can ensure that the carbon black will not fly and cause air pollution again.
Running this equipment that converts plastic waste into fuel can get 45-80% fuel, 20-50% carbon black, 5% combustible gas or no exhaust gas!!!
Fuel oil usage
(1) Waste plastic oil can be widely used in iron and steel, boiler plants, ceramics, electric power or chemical industries or hotel, hotel and other industries fuel oil, or for generating electricity generating units.
Carbon black usage
(2) Carbon black can be used for clay building bricks or as a fuel.
(3) Some combustible gases can be recycled to heat the reactor with fuel, which will save energy for the entire process.
Of course, the above is just an approximate figure, the pyrolysis rate of different types of waste plastics:
Raw Materials | Oil yield |
Waste plastic PE | 85%-95% |
PP | 80%-90% |
PS | 80%-90% |
ABS | 40% |
Pure white plastic | 60%-70% |
Fishing net, safety net | 45%-50% |
MAMEI | 40% |
Plastic brand | 20% |
Pulp | 20%-30% |
Daily Garbage | 30%-50% |
Pure plastic cable |
60%-80% |
Pure purchase package | 50% |
The reason why our equipment dared to use data to speak because he did have some outstanding advantages to ensure such a high rate of oil!
DoingGroup's pyrolysis plant
1. Using Q245R standard boiler plate steel, plate thickness up to 16mm, this plate can withstand high temperature, and because the head adopts curved design, strong pressure resistance, thus ensuring a longer service life.
2. The most advanced and most effective condenser in the oil industry. It can ensure that the oil and gas are cooled sufficiently to ensure the highest oil yield.
3. In addition to the oil-water separator, the series safety devices include water seals and vacuum devices. The function of the oil-water separator is to purify the oil and gas to prevent the backflow of oil and gas. The role of the water seal is to purify the exhaust gas and prevent the reverse flow of the exhaust gas. The role of the vacuum device is to provide negative pressure and drain oil and gas. In addition, the vacuum device can also increase the oil yield to ensure that the oil and gas are fully liquefied.
4. The unique welding process adopts a unique 3-step welding process to demonstrate DoingGroup's unremitting pursuit of perfect quality from the details.
In addition ,we offer the technology guidance at the installation spot, our engineer will not only help you to installation the equipment ,but also will test it!!Any question of the plastic pyrolysis plant,feel free to contact us!!
Technical parameter of converting plastic waste into fuel | ||||
---|---|---|---|---|
Items | Contents | |||
1 | Equipment type | DY-1-6 | DY-1-8 | DY-1-10 |
2 | Raw material | waste plastic, waste rubber, | ||
3 | Structural form | Horizontal rotation | Horizontal rotation | Horizontal rotation |
4 | 24-hour Capacity | 6 ton | 8 ton | 10 ton |
5 | Oil yield | 2.7-3.3ton | 3.6 -4.4ton | 4.5 -5.5ton |
6 | Operating pressure | Normal | Normal | Normal |
7 | Material of pyrolysis Reactor | Q245R | Q245R | Q245R |
8 | Thickness of pyrolysis Reactor | 16mm | 16mm | 16mm |
9 | Rotate speed of pyrolysis Reactor | 0.4turn/minute | 0.4turn/minute | 0.4turn/minute |
10 | Total power | 19KW | 19KW | 19KW |
11 | Mode of cooling | Water cooling | Water cooling | Water cooling |
12 | Cooling area of condenser | 100sqm | 100sqm | 100sqm |
13 | Kind of transmission | Internal gear drive | Internal gear drive | Internal gear drive |
14 | Noise dB(A) | ≤85 | ≤85 | ≤85 |
15 | Size of Reactor(D×L) | 2200×6000 | 2200×6600 | 2600×6600 |
16 | Working form | Intermittent operation | Intermittent operation | Intermittent operation |
17 | Delivery time | 20days | 20days | 20days |
18 | Weight | 27T | 30T | 35T |